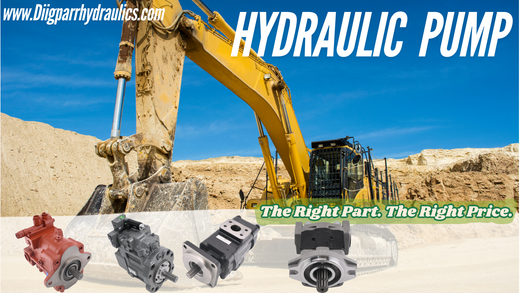
Essential Tips for Maintaining Your Hydraulic Pump: Ensuring Longevity and Efficiency
Hydraulic systems are at the heart of many industrial applications, powering everything from construction equipment to manufacturing machinery. One of the most crucial components of these systems is the hydraulic pump. Whether you're managing large-scale industrial operations or small-scale machinery, keeping your hydraulic pump in optimal condition is vital for system performance, efficiency, and longevity.
In this post, we’ll explore some key maintenance practices to help you ensure your hydraulic pump continues to perform efficiently and reliably over time. By following these tips, you can avoid unnecessary downtime, reduce repair costs, and extend the service life of your pump.
1. Regular Oil amp; Fluid Checks: The Foundation of Pump Health
Hydraulic pumps rely on fluid to operate smoothly, and maintaining proper oil levels and fluid quality is critical for their performance. Low oil levels, dirty fluid, or the wrong type of fluid can lead to excessive wear and potential failure of pump components.
What to do:
- Check oil levels regularly: Ensure that the hydraulic fluid is at the correct level. Low fluid levels can cause air to enter the system, leading to cavitation and pump damage.
- Monitor fluid cleanliness: Contaminants like dirt, metal particles, or moisture can cause significant damage. Use filtration systems to remove impurities and regularly change the fluid according to the manufacturer's recommendations.
- Use the right fluid: Always use the recommended hydraulic fluid for your specific pump model. The wrong fluid can result in poor performance and premature wear.
Pro Tip: Consider using a hydraulic fluid with anti-wear additives for better pump protection and to prevent damaging friction between moving parts.
2. Inspect and Clean Filters
Hydraulic systems often use filters to prevent contaminants from entering the pump. These filters need regular inspection and cleaning to ensure that they are functioning properly. A clogged or damaged filter can reduce flow, cause overheating, and ultimately lead to pump failure.
What to do:
- Check filters frequently: Inspect your filters for signs of dirt, debris, or damage. If the filter is clogged, replace it immediately.
- Clean filters regularly: Depending on the system’s usage, cleaning or replacing the filters every 500 to 1,000 operating hours is typically recommended. Refer to the manufacturer’s manual for specific guidance.
- Use high-quality filters: Ensure you are using the right type and size of filter for your system. Poor-quality filters can lead to contamination and reduced efficiency.
Pro Tip: Keep a log of filter inspections and replacements to stay on top of maintenance schedules.
3. Monitor Pressure and Flow Rates
The performance of a hydraulic pump is largely influenced by the pressure and flow rate within the system. Abnormal pressure levels can indicate potential issues, such as blockages, faulty valves, or pump wear.
What to do:
- Check pressure settings regularly: Ensure that the system pressure remains within the optimal range specified by the manufacturer. Operating outside of these limits can stress the pump and increase the risk of failure.
- Monitor flow rates: Sudden drops in flow rate or irregular pressure spikes can be a sign of wear or a blockage in the system. Both can impact pump efficiency and lead to system breakdowns.
Pro Tip: Install pressure gauges and flow meters to continuously monitor the pump's performance in real-time.
4. Lubricate Moving Parts
Hydraulic pumps contain various moving parts, including bearings and seals, which require proper lubrication to reduce friction and prevent wear. Over time, these parts can wear out, leading to leaks, excessive heat, and eventually, pump failure.
What to do:
- Lubricate bearings regularly: Depending on the type of hydraulic pump, ensure that bearings are well-lubricated with the appropriate grease. Lubricating moving parts reduces friction and prevents overheating.
- Check for leaks: Ensure that seals and gaskets are intact and not leaking fluid. Even small leaks can result in significant fluid loss, leading to performance degradation and even system damage.
- Maintain correct temperature: Keeping the pump at the right operating temperature is essential for reducing wear on moving parts. Overheating can accelerate seal degradation and cause premature pump failure.
Pro Tip: Use high-quality, manufacturer-approved lubricants to maximize protection for your pump's internal components.
5. Proper Alignment and Installation
Improper alignment and installation of a hydraulic pump can lead to misalignment, increased vibration, and excess wear. Ensuring that your pump is correctly installed and aligned is one of the simplest ways to prevent premature failure.
What to do:
- Check alignment regularly: Inspect the pump and motor alignment to ensure they are perfectly aligned. Misalignment can cause stress on the bearings and seals, resulting in damage over time.
- Ensure proper installation: Verify that the pump is mounted securely and that all connections are properly tightened. Loose fittings or mounting can cause vibrations and damage to the pump.
Pro Tip: Use laser alignment tools for precision when installing or realigning the pump.
6. Conduct Routine Performance Testing
In addition to regular inspections and maintenance, conducting routine performance tests can help you identify potential issues before they become serious problems. These tests can help you evaluate the overall health of the hydraulic pump and identify early signs of wear.
What to do:
- Perform load testing: Test the pump’s load-bearing capacity to ensure it is functioning within its specifications. Overloading the pump can cause overheating and premature failure.
- Analyze performance data: Use diagnostic tools to monitor the pump's efficiency and output. Any deviations from the standard operating parameters should be addressed promptly.
Pro Tip: Implementing predictive maintenance technology, like vibration analysis or temperature monitoring, can help you detect issues before they lead to failure.
7. Seek Professional Servicing When Needed
Despite all your efforts in routine maintenance, there may come a time when your pump needs professional attention. If you notice persistent issues such as unusual noises, vibrations, or decreased efficiency, it’s important to seek the help of a qualified technician.
What to do:
- Schedule professional inspections: Even with regular maintenance, occasional professional servicing is essential to ensure the pump is in top condition.
- Address issues promptly: Don’t wait for small issues to become big problems. Promptly addressing potential issues can save you time, money, and prevent extended downtime.
Conclusion: Keep Your Hydraulic Pump in Top Shape
Maintaining a hydraulic pump is critical to ensuring the reliability, efficiency, and longevity of your hydraulic system. Regular checks, fluid maintenance, and proper care can significantly extend the life of your pump while reducing the risk of costly repairs and downtime.
By following these essential tips, you’ll be able to get the most out of your hydraulic pump and ensure that your operations run smoothly for years to come.
Feel free to reach out to me for personalized consultation or to schedule a pump inspection. Share this article with your team to help them maintain the equipment they rely on every day!